Der Einsatz von Zerspanungswerkzeugen auf modernen Werkzeugmaschinen erfordert zur Aufrechterhaltung der geforderten Qualitäten einen regelmäßigen Werkzeugwechsel, da diese während der Werkstückbearbeitung verschleißen. Um ungeplante Maschinenstillstände und Ausschuss durch beschädigte Werkzeuge zu vermeiden, werden die Werkzeuge nach einer festgelegten Anzahl von Bearbeitungen ausgetauscht. Da der tatsächliche Verschleiß der Werkzeuge durch verschiedene Randbedingungen untereinander um bis zu 50 % schwanken kann, werden sie häufig zu früh getauscht, was zu Mehrkosten führt.
Der Werkzeugverschleißzustand lässt sich an speziellen Prüfplätzen mit optischen und taktilen Messmethoden ermitteln. Aus Aufwandsgründen wird dies in der Praxis jedoch kaum durchgeführt und stattdessen mit festen Werkzeugwechselintervallen gearbeitet. Einen neuen Ansatz stellt die Erkennung des tatsächlichen Verschleißzustandes durch die Auswertung verschiedener Messgrößen während des Bearbeitungsprozesses dar. Gemeinsam mit der GFE – Präzisionstechnik Schmalkalden GmbH haben KI-Trainer aus Ilmenau in diesem Projekt Möglichkeiten untersucht, eine dafür geeignete KI-basierte Lösung nachrüstbar und kostengünstig umzusetzen.
Motivation
Die Bearbeitungstechnologie Bohren ist eine sehr häufig angewendete und verbreitete Bearbeitung in der mechanischen Fertigung. Der Schneidenzustand der Bohrer hat dabei einen sehr hohen Einfluss auf die Effizienz der Bearbeitung und auf die Qualität der erzeugten Bohrung. Um eine prozesssichere Bearbeitung sicherzustellen, werden neue Schneidwerkzeuge für eine vordefinierte Zeitspanne verwendet, bevor sie ausgetauscht und ersetzt oder nachgearbeitet werden. Mit überwachenden Systemen werden die Intervalle der Regenerierung und der Austausch von Werkzeugen optimiert, indem der tatsächliche Verschleiß abgeschätzt und die verbleibende sogenannte Werkzeugstandzeit (d.h. die Zeit, die ein Werkzeug tatsächlich genutzt werden kann, bis es nachgeschliffen oder ausgetauscht werden muss) anhand einer Vielzahl von Prozessinformationen vorhergesagt wird.
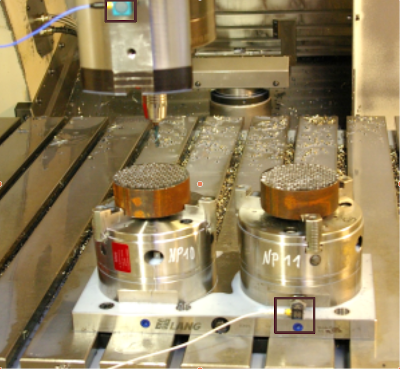
Abbildung 1: Messaufbau mit Sensoren im Bearbeitungsraum einer Zerspanungsmaschine (© Mittelstand 4.0-Kompetenzzentrum Ilmenau)
Daten für maschinelles Lernen
Im Projekt „KI-basierte Qualitätssicherung“ wurde die Zustandsprognose von Bohrern als Vorhersageproblem für die Reststandzeit (engl. remaining useful life – RUL) mit einem Multi-Beschleunigungssensor-Setup untersucht (Abbildung 1). Dabei galt es, folgende Fragen zu beantworten:
- Welche Sensorik ist für die Aufgabenstellung geeignet?
- Wo lässt sich mit vertretbarem Aufwand an Maschine, Werkzeug und Werkstück messen?
- Welche zusätzlichen Maschinenparameter sind relevant?
- Welche Signaleigenschaften müssen berücksichtigt werden?
- Welche maschinellen Lernmethoden sind für die Verarbeitung dieser Daten geeignet?
Mit einem geeigneten Messsetup wurden Versuche mit 64 identischen Bohrern durchgeführt, was etwa 130.000 Bohrungen entspricht. In Abbildung 2 ist die durch visuelle Inspektion ermittelte Verschleißentwicklung in Abhängigkeit von der Anzahl der durchgeführten Bohrungen für einen Bohrer dargestellt. Die bei der visuellen Inspektion erhaltenen Werte dienen später beim Training des KI-Modells als Referenzwerte (engl. ground truth).
Abbildung 2: Schneiden eines neuen (links) und eines verschlissenen Bohrers (rechts) (© Mittelstand 4.0-Kompetenzzentrum Ilmenau)
Die Verschleißentwicklung bei den einzelnen Bohrern ist sehr unterschiedlich. Die Auswertung der Verschleißentwicklung aller 64 Bohrer ergab für die konkret gewählten Versuchsparameter (Werkzeug- und Werkstückmaterial, Bohrungsdurchmesser und -tiefe, Drehzahl usw.) eine mittlere Standzeit der Bohrer von 2850 Bohrungen mit einer Standardabweichung von 1005 Bohrungen. Ein klassischer präventiver Ansatz könnte die durchschnittliche Standzeit von 2850 Bohrungen als Kriterium verwenden, bevor der Bohrer ausgetauscht wird. Die hohe Abweichung (40 % des Mittelwerts) bei den Standzeiten zeigt jedoch, dass ein solcher Ansatz aufgrund möglicher früherer Ausfälle sowie einer potenziell ineffizienten Ausnutzung der tatsächlichen RUL zu Mehrkosten führt.
Zur Datenerfassung kommen zwei 3-Achsen-Beschleunigungssensoren mit einer Samplerate von 5 kS/s an zwei verschiedenen Stellen zum Einsatz: zum einen am Spindelgehäuse der Maschine und zum anderen an der Spannvorrichtung für das Werkstück (Abbildung 1). Die Position an der Spindel wurde gewählt, weil dort während des gesamten Bearbeitungsprozesses ein relativ ähnliches Beschleunigungsverhalten unabhängig von der konkreten Position der Bohrung erwartet wurde. Im Projektverlauf zeigte sich jedoch, dass die Messdaten an dieser Stelle eine Vielzahl von Störungen beinhalten bzw. durch zahlreiche Nebenprozesse stark verrauscht sind. Dieses Problem war beim Sensor an der Werkstückspannvorrichtung in geringerem Maße vorhanden, jedoch variieren dort die Daten in Abhängigkeit von der Position der Bohrung auf dem Werkstück.
Geeignete Merkmale aus den Daten extrahieren
Für die erfolgreiche Entwicklung von KI-Modellen ist es wichtig, innerhalb der zur Verfügung stehenden Daten geeignete Merkmale zu identifizieren, auf deren Basis z.B. eine Zustandsklassifikation oder eine Regression ermöglicht wird. So mussten in diesem Projekt aus den Schwingungsmessdaten Merkmale extrahiert werden, deren Änderungen mit dem Verschleißzustand des Bohrers korrelieren. Solche Merkmale könnten z.B. in der Gesamtenergie oder im Zeit- und/oder Frequenzbereich des Schwingungssignals enthalten sein. Entsprechende Merkmalsextraktoren lassen sich hauptsächlich in zwei Kategorien einteilen: Zeitbereichsmerkmale (statistische Auswertungen der Energiepegel im Zeitbereich) und Frequenzbereichsmerkmale (spektrale Komponenten des Schwingungssignals). Als Beispiel für eines der im Projekt untersuchten Merkmale ist in Abbildung 3 der Verlauf des Merkmales Formfaktor (engl. shape factor) in Abhängigkeit von der Zahl der Bohrungen eines Bohrers dargestellt.
Abbildung 3: Normalisierter Formfaktor als Beispiel für ein relevantes Merkmal (© Mittelstand 4.0-Kompetenzzentrum Ilmenau)
Verschleißprognose mittels KI-Modell
Durch den kontinuierlichen Werkzeugverschleiß ist die angestrebte Prognose der verbleibenden Standzeit von Bohrern ein Regressionsproblem. Mittels einer Regressionsanalyse werden die extrahierten Merkmale an eine Funktion angepasst, deren Parameter für die extrahierten Merkmalsvektoren optimiert werden müssen. Dazu kam im Projekt ein künstliches neuronales Netz mit einer Architektur bestehend aus zwei vollständig verknüpften versteckten Schichten (jeweils 10 Neuronen unter Verwendung der Aktivierungsfunktion Rectified Linear Unit (ReLU)) zusammen mit einer Dropout-Schicht (0,5-Drop-Rate) zum Einsatz. Die Dropout-Schicht wurde hinzugefügt, um das Problem der Überanpassung während des Trainingsprozesses zu verhindern. Die Erhöhung der Anzahl der Schichten oder Neuronen führte nicht zu einer Steigerung der Schätzungsleistung. Die gewählte Architektur war dazu geeignet, die Nichtlinearität im Merkmalsraum zu erfassen. Eine ausführlichere Darstellung der Ergebnisse erfolgt u.a. auf dem internationalen IEEE Workshop „Metrology for Industry 4.0 and IoT“ vom 7.-9. Juni 2021.
Ergebnis
Im Projekt konnte gezeigt werden, dass durch den Einsatz geeigneter nachrüstbarer Sensorik und eine KI-basierte Datenauswertung eine deutliche Senkung der Werkzeugkosten in Zerspanungsprozessen ermöglicht wird. Der Schätzfehler bei der Bohrerreststandzeit beträgt im vorgestellten Beispiel ca. 500 Bohrungen und ist damit weniger als halb so groß wie beim herkömmlichen präventiven Ansatz. Dies ermöglicht eine um ca. 20% verbesserte Ausnutzung der Werkzeugstandzeit.
Das Mittelstand 4.0-Kompetenzzentrum Ilmenau unterstützt und informiert Unternehmen von der Projektidee bis zur Umsetzung und zeigt speziell auch Anwendungspotenziale für Technologien der künstlichen Intelligenz auf. Das vorgestellte Projekt wurde mit Unterstützung unserer KI-Trainer angegangen. Sprechen auch Sie uns gerne an. Mehr Infos gibt es auch in der Projektbeschreibung.
Ansprechpartner:
Wolfram Kattanek
KI-Trainer
Telefon: 03677/8749344
E-Mail: kattanek@kompetenzzentrum-ilmenau.de
Bildquellen
- Messaufbau: © Mittelstand-Digital Zentrum Ilmenau
- Verschleiß am Werkzeug: © Mittelstand-Digital Zentrum Ilmenau
- Sensordaten: © Mittelstand-Digital Zentrum Ilmenau